Mastering Industrial Blower Design for Enhanced Performance
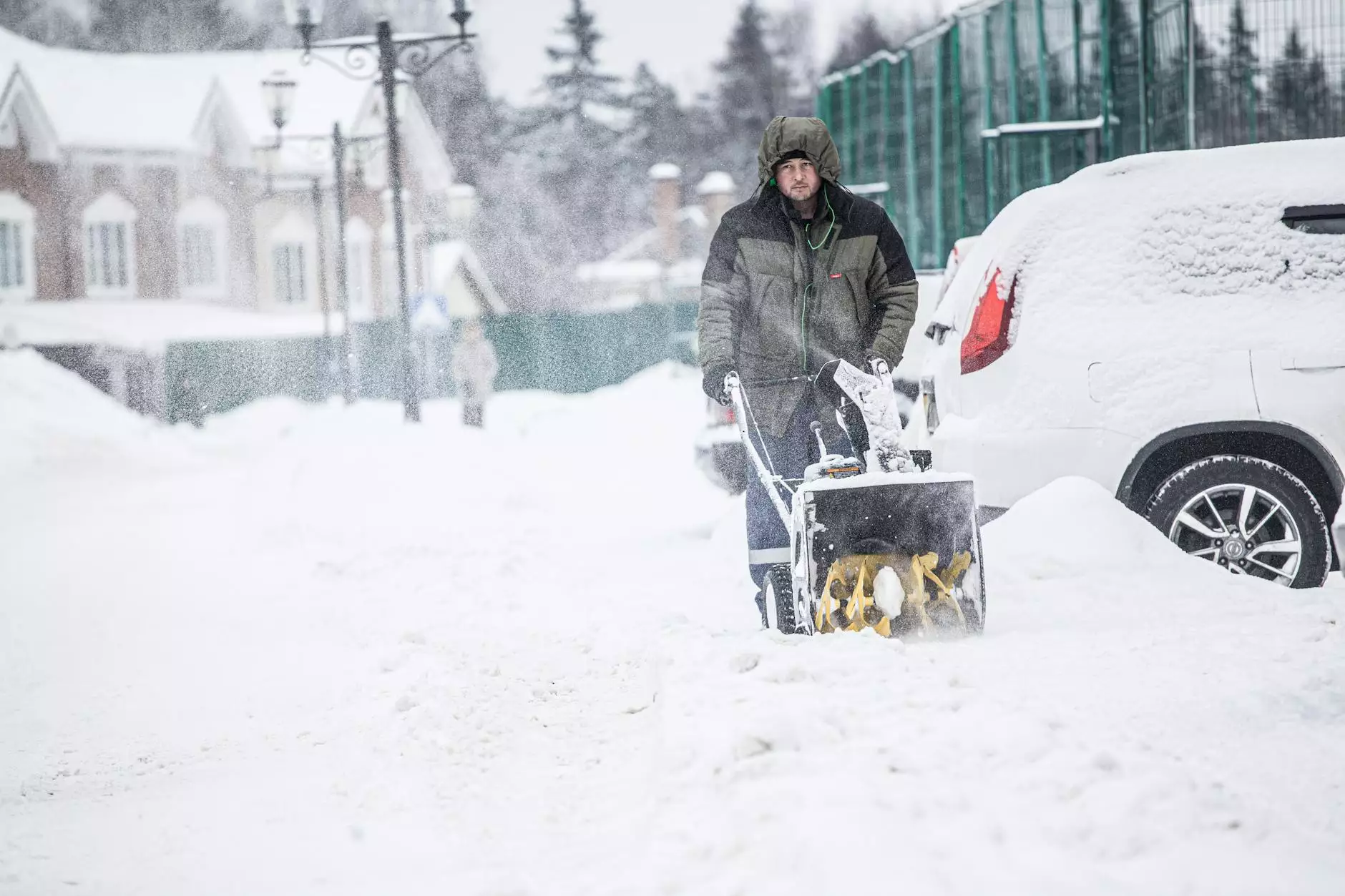
In the realm of industrial applications, the design of blowers holds immense significance, especially in Blow Dry/Out Services. An industrial blower is a crucial component used across various industries for moving air or gas. Understanding the intricacies of industrial blower design can lead to improved efficiency, reduced costs, and superior operational effectiveness. In this comprehensive article, we will explore every aspect of industrial blower design, its types, applications, and best practices.
Understanding Industrial Blowers
Before delving into the design elements, it is essential to understand what industrial blowers are. These devices are essential for various tasks, including:
- Ventilation: Providing adequate airflow in confined spaces.
- Drying: Facilitating the removal of moisture from products and components.
- Transporting Materials: Moving powders, granules, and other materials in manufacturing processes.
- Cooling: Assisting in the cooling of equipment and processes.
The Importance of Industrial Blower Design
The design of an industrial blower impacts its performance, efficiency, and longevity. A well-designed blower can significantly affect energy consumption, maintenance costs, and production efficiency. Here’s why meticulous industrial blower design matters:
- Energy Efficiency: Proper design minimizes energy consumption and boosts output.
- Operational Reliability: A robust design ensures reliable operation in demanding conditions.
- Maintenance Ease: Thoughtful design can ease maintenance and servicing tasks.
- Performance Optimization: Tailored designs can enhance performance metrics across various tasks.
Key Components of Industrial Blower Design
To achieve optimal performance, the following components are vital in industrial blower design:
1. Housing and Enclosure
The housing of the blower protects internal components and must be designed to withstand the operational environment. The material choice, shape, and size all influence airflow patterns and overall performance.
2. Impeller
The impeller is the heart of the blower, responsible for moving air. It must be designed to optimize performance and efficiency, considering factors like:
- Blade Shape: Varying blade shapes can have different effects on airflow and pressure.
- Diameter: A larger impeller can move more air, but may require more energy to operate.
- Material: Durable materials can withstand wear and tear and prolong the blower's life.
3. Motor
The motor drives the impeller, and its selection must align with the blower’s design. This includes considerations of power, efficiency, and compatibility with the motor control system.
4. Airflow Path
Efficient airflow pathways reduce turbulence, which can hinder performance. The design must ensure smooth transitions and minimal bends in the airflow path to enhance efficiency.
Types of Industrial Blowers
Industrial blowers come in various types, each serving different applications. Understanding these types can inform better design practices:
1. Centrifugal Blowers
Centrifugal blowers create airflow by converting rotational energy from the impeller into kinetic energy. These are characterized by:
- High Efficiency: Excellent for moving large volumes of air at low pressures.
- Versatile Applications: Used in HVAC systems, material handling, and drying processes.
2. Positive Displacement Blowers
Positive displacement blowers trap a fixed volume of air and then force it out. Their benefits include:
- Consistency: Provides a steady pressure irrespective of changes in discharge conditions.
- High Pressure: Suitable for applications requiring high pressure.
Applications of Industrial Blowers in Blow Dry/Out Services
In the context of Blow Dry/Out Services, industrial blowers have diverse applications. Let's explore a few:
1. Hairdressing Salons
In salons, blow dryers powered by industrial blowers help achieve flawless hairstyles quickly. The design must ensure balanced airflow for efficient drying without damaging hair.
2. Manufacturing Processes
Blowers are pivotal in the drying of materials in manufacturing. An optimized airflow ensures uniform moisture removal, enhancing the quality of the final product.
3. Environmental Control
In facilities where particulate matter is prevalent, blowers maintain air quality by circulating clean air. Proper design ensures efficient removal of contaminants while minimizing energy usage.
Best Practices for Industrial Blower Design
To create an effective industrial blower design, consider the following best practices:
1. Conduct a Thorough Needs Assessment
Understanding the specific requirements of your application can help in customizing the blower design. Factors to consider include airflow requirements, pressure settings, and operational conditions.
2. Use Quality Materials
Material selection influences durability and performance. Opt for materials that resist corrosion, abrasion, and wear to extend the blower's life.
3. Optimize Energy Use
Integrate energy-efficient components and systems. For example, variable frequency drives (VFDs) can help to adjust airflow according to real-time needs, saving energy.
4. Implement Advanced Design Software
Utilize state-of-the-art design software that simulates airflow and predicts performance under various conditions. This allows for precision in the design process.
5. Prioritize Safety Standards
Ensure that the design adheres to industry safety standards. This includes features like vibration dampening and thermal management to prevent operational hazards.
The Future of Industrial Blower Design
The evolution of technology continues to shape industrial blower design. Future trends may include:
- Smart Blowers: Integration of IoT technology for real-time monitoring and automation.
- Sustainable Materials: Using biodegradable or recyclable materials for blower fabrication.
- Energy Harvesting: Designs that harness energy from operational waste or environmental sources.
Conclusion
The art of industrial blower design is essential for optimizing performance in various sectors, notably in Blow Dry/Out Services. By understanding the critical components, applications, and best practices, industries can achieve superior efficiency and reliability. As technology continues to evolve, staying abreast of new developments will ensure that businesses remain competitive and capable of meeting the demands of a dynamic marketplace.
For businesses looking to invest in reliable and efficient blower systems, partnering with experts like TMM can provide invaluable insights and guidance. The right designs and strategies can pave the way for enhanced service delivery and customer satisfaction.