Unlocking Potential: The Role of the CNC Parts Factory in Modern Manufacturing
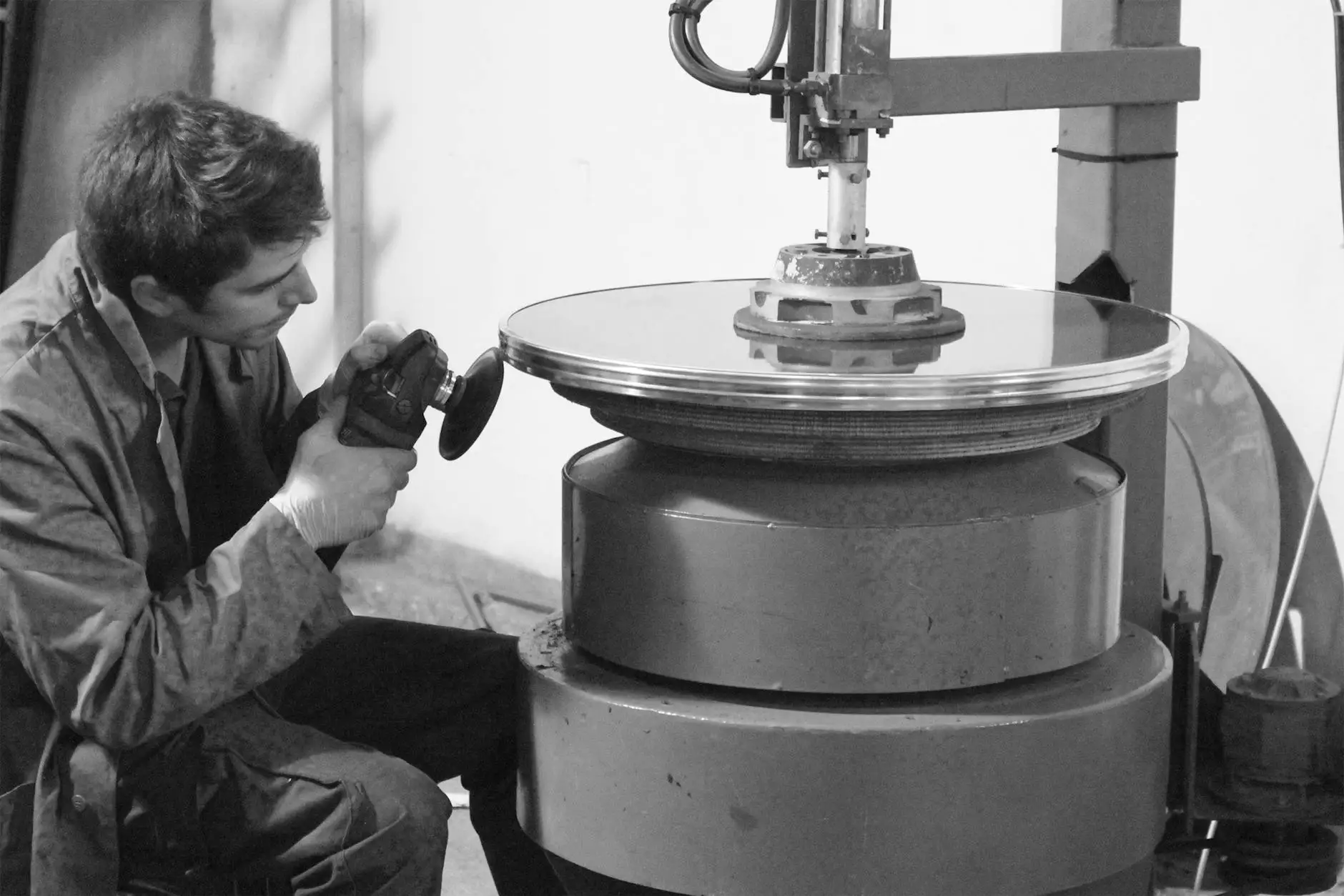
The landscape of manufacturing is constantly evolving, and at the heart of this transformation is the cnc parts factory. These facilities are not just hubs of production; they are the engines of innovation, efficiency, and high-quality craftsmanship. Understanding their significance and operational intricacies can provide insights into the future of industrial manufacturing.
What is a CNC Parts Factory?
A cnc parts factory utilizes Computer Numerical Control (CNC) technology to produce a wide array of components with precision and accuracy. This technology employs computer programs to control the movement of machinery, enabling the creation of complex and intricate parts inadvertently impossible with manual manufacturing processes.
- Precision: CNC machines can produce parts to very tight tolerances, often within a few micrometers.
- Consistency: Once a design is programmed, the machines can replicate parts exactly every time, minimizing variations and errors.
- Flexibility: CNC technology allows for quick changes in design and production runs, making it easy to adapt to new projects.
- Efficiency: Automated processes reduce the time required for production while maintaining high quality.
The Importance of CNC Parts Factories in Various Industries
CNC parts factories serve a myriad of sectors, making them a cornerstone of modern manufacturing. Here are some industries where these facilities play a crucial role:
Aerospace Industry
The aerospace sector requires parts that meet stringent safety and quality standards. A cnc parts factory is essential to producing components such as engine brackets, landing gear parts, and control surfaces with unparalleled precision.
Automotive Industry
As an ever-evolving field, the automotive industry relies heavily on CNC manufacturing. From engine components to intricate dashboard designs, CNC technology helps in producing reliable parts that enhance vehicle performance and safety.
Medical Devices
Critical devices in healthcare, such as surgical instruments and implants, are manufactured in CNC parts factories. The accuracy and reliability of these parts can significantly impact patient outcomes.
Benefits of CNC Parts Manufacturing
The transition towards CNC manufacturing offers several advantages. Here are some key benefits :
- Cost Efficiency: While the initial setup costs can be high, CNC manufacturing reduces labor costs and waste, leading to long-term savings.
- High Production Rates: CNC machines can operate continuously, producing a significant volume of parts in a short amount of time.
- Enhances Innovation: CAD/CAM software integration allows designers and engineers to innovate rapidly, pushing the boundaries of product development.
- Quality Assurance: With advanced monitoring systems, defects can be caught early, ensuring only the highest quality products leave the factory.
Technological Advancements in CNC Parts Factories
The world of CNC manufacturing is continually advancing. Some of the most exciting technological trends include:
Automation and Robotics
Many CNC parts factories are incorporating robotics to streamline production processes. Automated systems can handle material loading, unloading, and even quality inspection, improving efficiency significantly.
Additive Manufacturing Integration
Combining CNC machining with additive manufacturing techniques, such as 3D printing, allows factories to produce complex geometries that were previously inconceivable. This synergy enhances the ability to create parts that are lighter yet just as strong.
Artificial Intelligence and Machine Learning
With AI and machine learning, CNC machines are becoming smarter. They can predict failures, optimize processes, and facilitate real-time adjustments, all contributing to smoother operations.
Quality Control in CNC Parts Factories
Quality control is non-negotiable in the cnc parts factory. The precision required in manufacturing components means that rigorous testing and inspection processes must be in place. Some methods include:
- Dimensional Inspection: Measuring physical dimensions to ensure they meet specified tolerances.
- Non-Destructive Testing: Techniques such as ultrasonic testing for detecting internal flaws without damaging the part.
- Visual Inspection: Trained technicians conducting visual assessments for surface consistency and anomalies.
- Statistical Process Control: Utilizing statistical methods to monitor and control the manufacturing process.
Conclusion
The significance of a cnc parts factory in the modern manufacturing landscape cannot be overstated. As industries demand higher quality, faster production times, and innovative design capabilities, CNC technology stands at the forefront of these changes. With continuous advancements in technology and methodology, CNC parts factories are poised to shape the future of manufacturing across a plethora of industries.
For businesses looking to leverage the benefits of CNC manufacturing, partnering with a reputable cnc parts factory is essential. Recognizing the endless possibilities this technology provides will not only improve production processes but also enhance the overall quality of products in a competitive marketplace.
Learn more about how Deep Mould can lead your manufacturing endeavors forward, ensuring efficiency and exceptional quality every step of the way.